Combining flexible and rigid materials into a single movable component without assembly
This is a seed phase project lasting from 6 up to 9 months.
The global COVID-19 pandemic highlighted the need for flexible and adaptive production. Especially Additive Manufacturing (AM) of medical and personal safety equipment like protective visors and respirators showed, that the period from the collapse of global supply chains to the local industrial production can be bridged by AM.
Additive Manufacturing offers the possibility to quickly and cost-effectively develop new laboratory equipment, which is indispensable for research in the chemical and pharmaceutical sector. To guarantee the operational readiness of these laboratory aids without additional process steps the number of structural parts such as bolts, gear or hinges must be minimized. The necessary functional integration can be achieved, for example, by using multi-material components made from a combination of rigid and flexible materials. However, this decisive advantage is currently limited by the fact that most polymeric materials available for Additive Manufacturing are incompatible with each other.
The ALaRM project investigates which design or process-related measures can be taken to ensure a sufficient physical or mechanical bonding. The focus is set on alternative resources independent from oil, such as locally producible biopolymers whose compatibility with standard plastics has not been intensively researched yet.
#Multi-Material Additive Manufacturing #Biopolymers #Multi-scale texturation #Numerical modelling
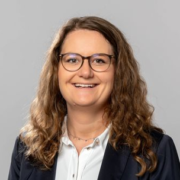
Additive Manufacturing opens new outstanding ways to design, produce, and use products, which inevitably changes how we live our everyday life. It is our responsibility to guide this technology into a sustainable future.
Our goals
- Manual for maker community: The establishment of a scientific framework of recommended actions from the material selections to the design and the production of Multi-Materials (MM) parts for everyday users of AM. Besides standard materials, biopolymers are examined towards their design conception and mechanical performance and evaluated towards their ability as sustainable alternatives.
- Functional Integration: The analysis of the chemo-physico-thermomechanical bonding between different materials in AM through a hierarchical experimental approach:
– micro-scale: analysis of the connection between two strands of the same material
– multi-meso-scale: examination of two different materials - Improvement of process comprehension and numerical modeling: Multi-material-parts exhibit anisotropic properties (micro-texturation, residual deformation, void, mechanical response, etc.) caused by different materials and deposition trajectories. The examination of the physics of structuration, crystallization, gelation and adhesion between the layers is essential for the exact adjustment of process parameters and the development of new materials and structures.
Investigators

Prof. Dr.-Ing. Katrin Wudy
Joseph Hofmann, M.Sc
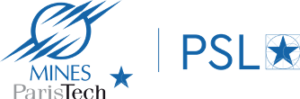